Servo Motor Repair
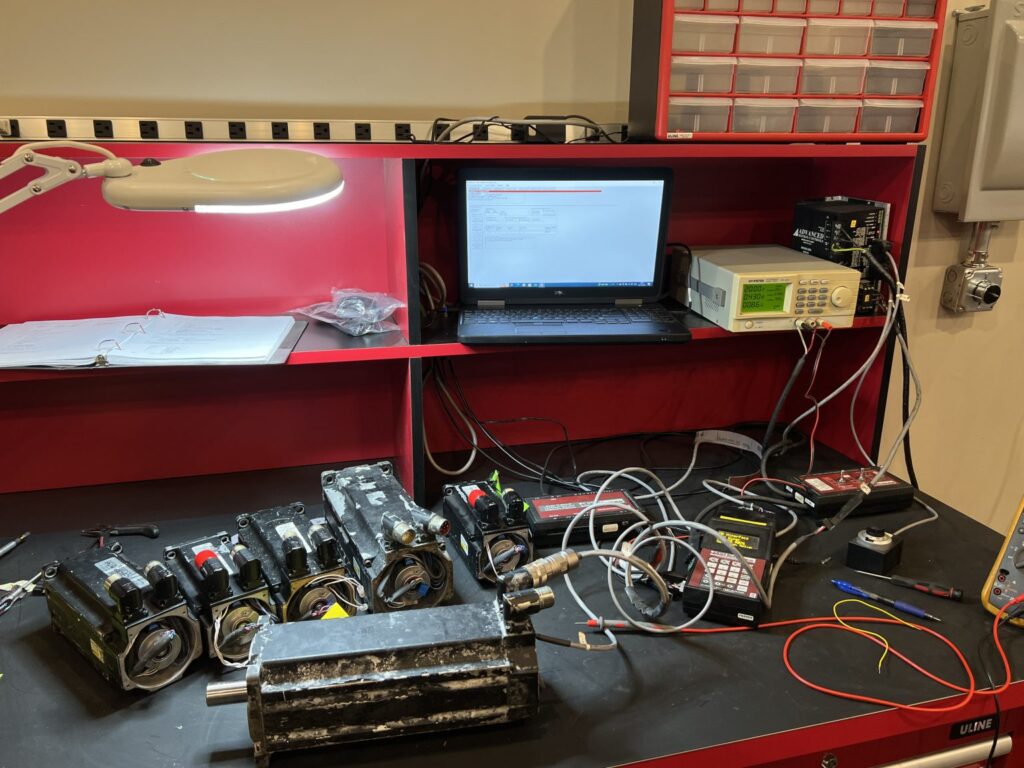
At Omega Industrial Repair, we take pride in our meticulous and comprehensive servo motor repair process, which is carefully executed by our certified technicians. Our step-by-step process ensures that your servo motors receive exceptional care and attention, resulting in reliable and efficient performance.
Our commitment to delivering quality servo motor repair services goes beyond the repair process itself. We stock thousands of parts, which enables us to avoid ordering delays and offer free rush turnarounds in 24 to 48 hours for emergencies, ensuring minimal downtime for your operations.
Using cutting-edge technology in our testing procedures, we can detect even the tiniest, hard-to-find flaws in your servo motors. Additionally, our comprehensive approach involves testing various failure-prone components, not just the ones currently causing issues, and provide you with the peace of mind of an 18-month in-service warranty for the entire motor.
At Omega Industrial Repair, you’ll find transparent pricing and reasonable repair costs, empowering you to make informed decisions about equipment maintenance without any unexpected fees or surprises.
Select Omega Industrial Repair for dependable, top-notch servo motor repair services that guarantee your equipment’s long-term optimal and efficient performance.
Get a Free Quotes
An overview of our servo motor repair process
At Omega Industrial Repair, we are committed to providing top-notch industrial electric motor repair services. Trust us to keep your motors performing at their best and to minimize downtime in your operations. Request a quote today to experience the benefits of our expertise and reliable repair processes!
Visual Inspection
Our technicians begin by conducting a thorough visual inspection of the servo motor, looking for any obvious failures such as burn marks, corrosion, fractures, and poor connections.
Feedback Cover Examination
The feedback cover is carefully removed, and the device is closely examined. Electrical tests are performed to determine if the feedback can be safely powered. During this stage, the feedback is also disconnected to inspect the motor windings without causing any damage.
Motor Windings Testing
Using an advanced AWA analyzer, we perform megger, high potential, resistance balance, and surge testing on the motor windings to identify any potential issues.
Magnet Utilization Testing
In the case of servo motors utilizing magnets, KE or voltage constant tests are conducted to ensure their proper functioning.
Machine Work and Component Replacement
If needed, we carry out essential machine work, such as keyway and shaft repair, as well as bearing journal work. New bearings and sealing components are installed in every repair to enhance performance and longevity.
Feedback Testing
The feedback component, whether it be resolver, encoder, or tachometer, is meticulously tested using the Mitchell electronic system. If any faults are detected, we promptly repair or replace the feedback device.
Why Choose Omega Industrial Repair
- Expert Technicians: Our team of skilled technicians has in-depth knowledge and experience in repairing a wide range of industrial electronic equipment.
- Quick Turnaround: We understand the importance of minimizing downtime in industrial settings. Our streamlined repair process ensures quick turnaround times without compromising on quality.
- Quality Assurance: We are committed to providing top-notch repairs, and all our services undergo rigorous testing to ensure they meet the highest industry standards.
- Cost-Effective Solutions: Our focus is on providing cost-effective solutions to our clients. We aim to extend the life of your equipment and help you avoid unnecessary replacements.
- Wide Manufacturer Coverage: We can repair equipment from various manufacturers, making us your one-stop-shop for industrial electronic repair needs.
- Customer Satisfaction: Our priority is customer satisfaction. We work closely with our clients, keeping them informed throughout the repair process.
Our Services